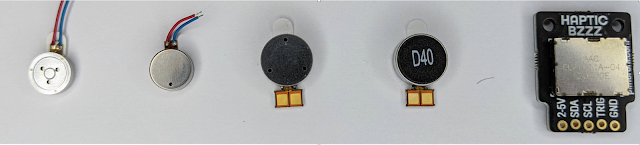
Haptics with Input: Using Linear Resonant Actuators for Sensing
November 18, 2020
Posted by Artem Dementyev, Hardware Engineer, Google Research
Quick links
As wearables and handheld devices decrease in size, haptics become an increasingly vital channel for feedback, be it through silent alerts or a subtle "click" sensation when pressing buttons on a touch screen. Haptic feedback, ubiquitous in nearly all wearable devices and mobile phones, is commonly enabled by a linear resonant actuator (LRA), a small linear motor that leverages resonance to provide a strong haptic signal in a small package. However, the touch and pressure sensing needed to activate the haptic feedback tend to depend on additional, separate hardware which increases the price, size and complexity of the system.
In “Haptics with Input: Back-EMF in Linear Resonant Actuators to Enable Touch, Pressure and Environmental Awareness”, presented at ACM UIST 2020, we demonstrate that widely available LRAs can sense a wide range of external information, such as touch, tap and pressure, in addition to being able to relay information about contact with the skin, objects and surfaces. We achieve this with off-the-shelf LRAs by multiplexing the actuation with short pulses of custom waveforms that are designed to enable sensing using the back-EMF voltage. We demonstrate the potential of this approach to enable expressive discrete buttons and vibrotactile interfaces and show how the approach could bring rich sensing opportunities to integrated haptics modules in mobile devices, increasing sensing capabilities with fewer components. Our technique is potentially compatible with many existing LRA drivers, as they already employ back-EMF sensing for autotuning of the vibration frequency.
![]() |
Different off-the-shelf LRAs that work using this technique. |
Back-EMF Principle in an LRA
Inside the LRA enclosure is a magnet attached to a small mass, both moving freely on a spring. The magnet moves in response to the excitation voltage introduced by the voice coil. The motion of the oscillating mass produces a counter-electromotive force, or back-EMF, which is a voltage proportional to the rate of change of magnetic flux. A greater oscillation speed creates a larger back-EMF voltage, while a stationary mass generates zero back-EMF voltage.
![]() |
Anatomy of the LRA. |
Active Back-EMF for Sensing
Touching or making contact with the LRA during vibration changes the velocity of the interior mass, as energy is dissipated into the contact object. This works well with soft materials that deform under pressure, such as the human body. A finger, for example, absorbs different amounts of energy depending on the contact force as it flattens against the LRA. By driving the LRA with small amounts of energy, we can measure this phenomenon using the back-EMF voltage. Because leveraging the back-EMF behavior for sensing is an active process, the key insight that enabled this work was the design of a custom, off-resonance driver waveform that allows continuous sensing while minimizing vibrations, sound and power consumption.
![]() |
Touch and pressure sensing on the LRA. |
We measure back-EMF from the floating voltage between the two LRA leads, which requires disconnecting the motor driver briefly to avoid disturbances. While the driver is disconnected, the mass is still oscillating inside the LRA, producing an oscillating back-EMF voltage. Because commercial back-EMF sensing LRA drivers do not provide the raw data, we designed a custom circuit that is able to pick up and amplify small back-EMF voltage. We also generated custom drive pulses that minimize vibrations and energy consumption.
![]() |
Simplified schematic of the LRA driver and the back-EMF measurement circuit for active sensing. |
Applications
The behavior of the LRAs used in mobile phones is the same, whether they are on a table, on a soft surface, or hand held. This may cause problems, as a vibrating phone could slide off a glass table or emit loud and unnecessary vibrating sounds. Ideally, the LRA on a phone would automatically adjust based on its environment. We demonstrate our approach for sensing using the LRA back-EMF technique by wiring directly to a Pixel 4’s LRA, and then classifying whether the phone is held in hand, placed on a soft surface (foam), or placed on a table.
![]() |
Sensing phone surroundings. |
We also present a prototype that demonstrates how LRAs could be used as combined input/output devices in portable electronics. We attached two LRAs, one on the left and one on the right side of a phone. The buttons provide tap, touch, and pressure sensing. They are also programmed to provide haptic feedback, once the touch is detected.
![]() |
Pressure-sensitive side buttons. |
There are a number of wearable tactile aid devices, such as sleeves, vests, and bracelets. To transmit tactile feedback to the skin with consistent force, the tactor has to apply the right pressure; it can not be too loose or too tight. Currently, the typical way to do so is through manual adjustment, which can be inconsistent and lacks measurable feedback. We show how the LRA back-EMF technique can be used to continuously monitor the fit bracelet device and prompt the user if it's too tight, too loose, or just right.
![]() |
Fit sensing bracelet. |
Evaluating an LRA as a Sensor
The LRA works well as a pressure sensor, because it has a quadratic response to the force magnitude during touch. Our method works for all five off-the-shelf LRA types that we evaluated. Because the typical power consumption is only 4.27 mA, all-day sensing would only reduce the battery life of a Pixel 4 phone from 25 to 24 hours. The power consumption can be greatly reduced by using low-power amplifiers and employing active sensing only when needed, such as when the phone is active and interacting with the user.
![]() |
Back-EMF voltage changes when pressure is applied with a finger. |
The challenge with active sensing is to minimize vibrations, so they are not perceptible when touching and do not produce audible sound. We optimize the active sensing to produce only 2 dB of sound and 0.45 m/s2 peak-to-peak acceleration, which is just barely perceptible by finger and is quiet, in contrast to the regular 8.49 m/s2 .
Future Work and Conclusion
To see the work presented here in action, please see the video below.
In the future, we plan to explore other sensing techniques, perhaps measuring the current could be an alternative approach. Also, using machine learning could potentially improve the sensing and provide more accurate classification of the complex back-EMF patterns. Our method could be developed further to enable closed-loop feedback with the actuator and sensor, which would allow the actuator to provide the same force, regardless of external conditions.
We believe that this work opens up new opportunities for leveraging existing ubiquitous hardware to provide rich interactions and closed-loop feedback haptic actuators.
Acknowledgments
This work was done by Artem Dementyev, Alex Olwal, and Richard Lyon. Thanks to Mathieu Le Goc and Thad Starner for feedback on the paper.